VT Economic Development Faculty Assist in Strengthening Rural Manufacturing
April 4, 2019
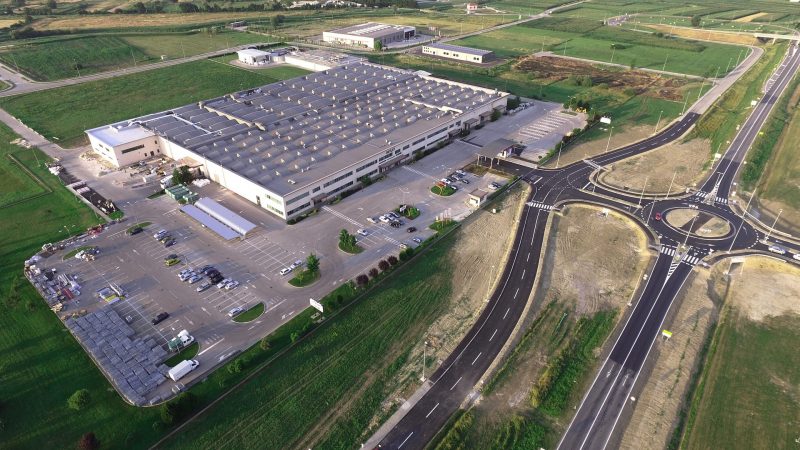
Manufacturing is essential to the economy of the United States. Manufactured goods comprise half of U.S. exports and 11.6 percent of U.S. economic output. Retaining and growing rural manufacturing jobs is a pressing concern for national, state, and local policy-makers. Yet, small to midsize manufacturers in rural regions lag behind larger firms and those in more urban regions in terms of revenue and job growth.
Rural manufacturers are unable to keep up as the manufacturing industry moves to larger production units, reducing workforce needs and shifting the market from rural regions to urban centers.
While there are services out there meant to assist manufacturers in gaining a qualified workforce and enhancing their services, many do not access these resources meant to help them adapt to economic changes.
In their research published in the February edition of the Economic Development Quarterly, Virginia Tech Office of Economic Development faculty Sarah Lyon-Hill, Margaret Cowell, Scott Tate, and Albert Alwang, explored how companies access available support resources and identified ways to reduce the barriers to greater utilization of assistance services and expertise in southwestern Virginia. These providers work in conjunction with regional economic restructuring efforts at the regional, state, and federal levels. This work is part of a U.S. Department of Labor-funded project, to strengthen connections between workforce resource organizations and employers in the manufacturing sector.
VT researchers surveyed and interviewed manufacturers to better understand this phenomenon. The study confirmed the underutilization of assistance resources stemmed from a lack of information and awareness about resources. Manufacturers reported the perception that their company’s needs might be too specialized for generic assistance programs, trainings were too far from their location, and that some felt they had little decision making power within their parent company to adopt assistance processes and improvements.
Albert Alwang noted, that some of the manufactures remaining in southwest Virginia described a feeling of being lefts behind. “As economic shifts hinder individual companies, the whole regional network of manufacturers suffers. The support and communication networks that once held these economies and communities together are damaged,” stated Alwang.
Although, workforce development and technical assistance organizations create programming aimed at supporting manufacturers through these challenging economic conditions, the networks needed to connect industry, public sector, and non-profit resource providers have been weakened, as rural manufacturing has declined in terms of overall numbers.
The research team recommended strategies for workforce development and technical assistance providers to better communicate with companies, and to offer services tailored to individual firm needs or shared needs among smaller groups of manufacturers.
Sarah Lyon-Hill explained, “The impact of accessing these resources could be significant for the manufacturing industry. The point of this research was to identify the missing components that better connect manufacturers with these support services. I am hopeful that with research like this, these two groups may form more beneficial and lasting partnerships, contributing to a rejuvenated economic landscape for the U.S. manufacturing industry.”
Written By Jennifer Morgan